Overcoming Boundaries: Innovations in Multi-Material Injectable Casting
Lately, the world of manufacturing has witnessed a remarkable change, especially in the field of injection plastics. As industries strive for enhanced productivity and sustainability, advancements in multi-material injection molding have emerged as a powerful approach to meet these demands. This advanced technique facilitates the combination of different materials into a single process, paving the way for the creation of sophisticated designs and improved product functions.
Molders are at the forefront of this revolution, harnessing new techniques and practices to dismantle traditional barriers. By combining different materials, companies can manufacture lighter, more robust, and increasingly flexible products that address a varied range of applications. As we delve into the thrilling progress in multi-material molding, we will discover the tactics and technologies that are transforming the environment of modern manufacturing.
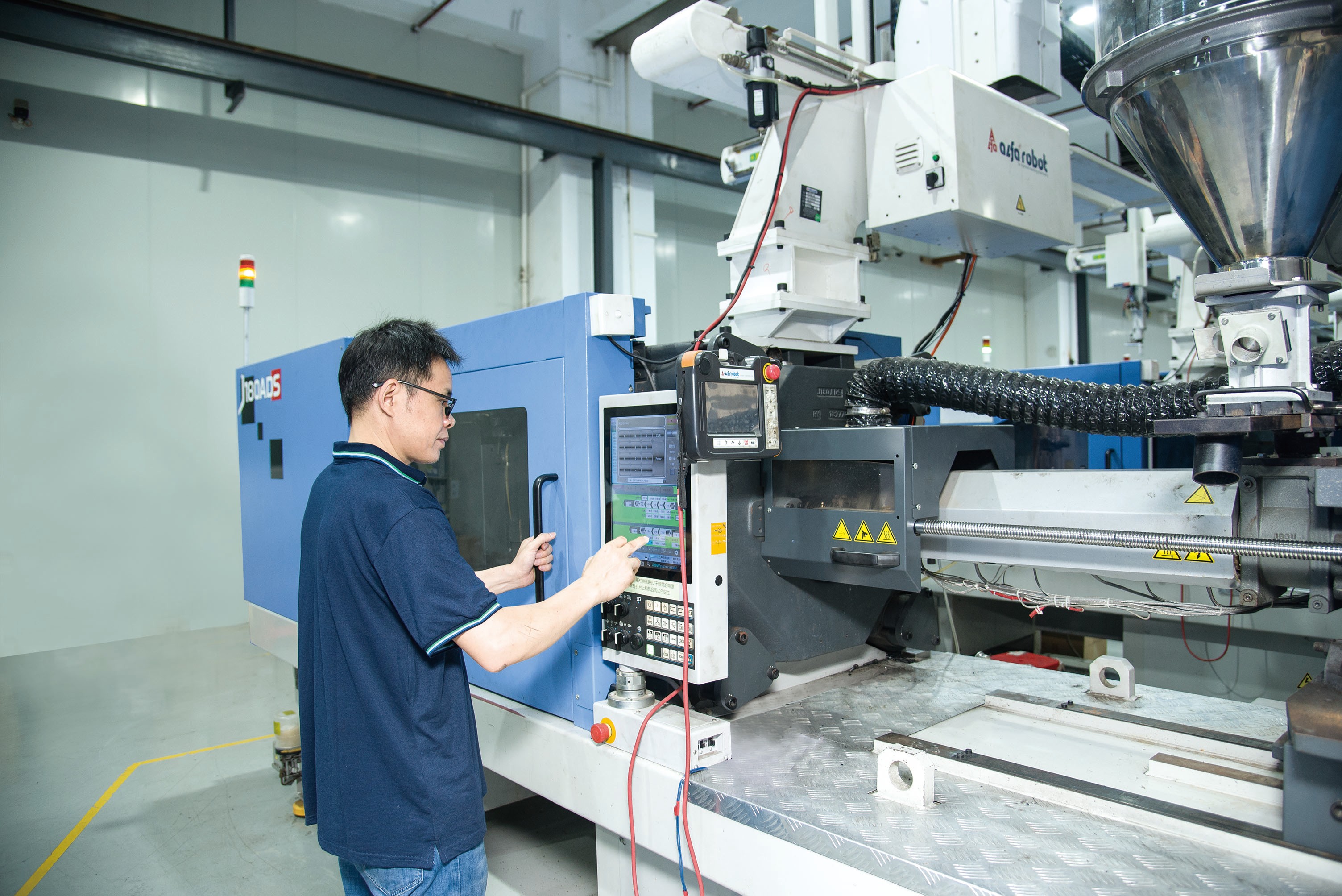
Progress in Multi-Material Methods
The area of injection-molding has experienced significant progress in multi-material methods, fueling the creation of more complex and practical products. These developments enable manufacturers to combine different materials in a unified molding process, allowing for superior product performance and aesthetic appeal. This functionality simplifies production and reduces material waste, complying with modern sustainability objectives.
Recent technologies have introduced the use of co-injection and over-molding processes, facilitating the integration of solid and compliant materials into one integrated whole. This is particularly advantageous in industries like healthcare and consumer electronics, where a combination of durability and ease is essential. For example, the capability to form materials with diverse attributes provides new avenues for creating comfortable designs that meet consumer demands.
In addition, developments in digital design and simulation programs have significantly enhanced the planning and execution of multi-material injection molding initiatives. These applications support manufacturers in forecasting material performance and optimizing the molding process, which yields higher quality products and shortened cycle times. As these technologies continue to evolve, we can expect an even broader implementation of composite methods across various fields.
Obstacles in Implementation
Executing multiple-material injection molding presents a number of technical challenges that manufacturers must tackle. One significant problem is the harmonization of various materials used in the method. Each material has unique thermal and flow characteristics, which can lead to problems in achieving consistent melt and proper adhesion between layers. If not properly managed, this can lead to structural weaknesses and product failures.
An additional challenge lies in the complexity of the machinery required for multi-material injection molding. Injection molders need cutting-edge technology capable of processing multiple materials effectively. This requires substantial capital in new equipment and alterations to present systems. Many manufacturers face barriers in retraining their staff to effectively operate these complex machines, leading to potential setbacks and increased production costs.
Moreover, the design phase must be thoroughly planned to ensure that multiple-material parts meet operational and aesthetic requirements. Designers must take into account how materials will function during the molding process, as well as how they will perform in real-world applications. This need for careful planning can complicate projects and extend development deadlines, posing a difficulty for companies eager to innovate and bring new products to market quickly.
Future Trends in Injection Molding
The future of injection molding is poised to be transformed by advancements in automated systems and smart technology. As manufacturers seek to improve efficiency and lower costs, the integration of Industry 4.0 principles will become more prevalent. Smart injection molder s fitted with IoT technology will facilitate real-time monitoring of processes, leading to enhanced predictive maintenance and reduced downtime. This shift towards automation assists manufacturers optimize production schedules and respond quickly to market demands.
Eco-friendliness will play a significant role in shaping the future of injection molding. With heightened pressure to reduce waste and lower environmental impact, advancements in materials and processes will arise. Biodegradable plastics and recycled materials are projected to gain traction, complemented by energy-efficient molding techniques. These advancements will both support environmental goals but also align with consumer preferences for sustainable products.
Tailoring and personalization will drive the need for more flexible injection molding solutions. As industries shift towards smaller production runs of specialized products, injection molders will need to adapt their techniques to accommodate this change. The emergence of digital fabrication technologies, such as 3D printing and hybrid systems, will enable increased flexibility in design and production processes. This trend will empower manufacturers to create intricate geometries and multi-material components, fulfilling varied consumer needs while boosting product performance.